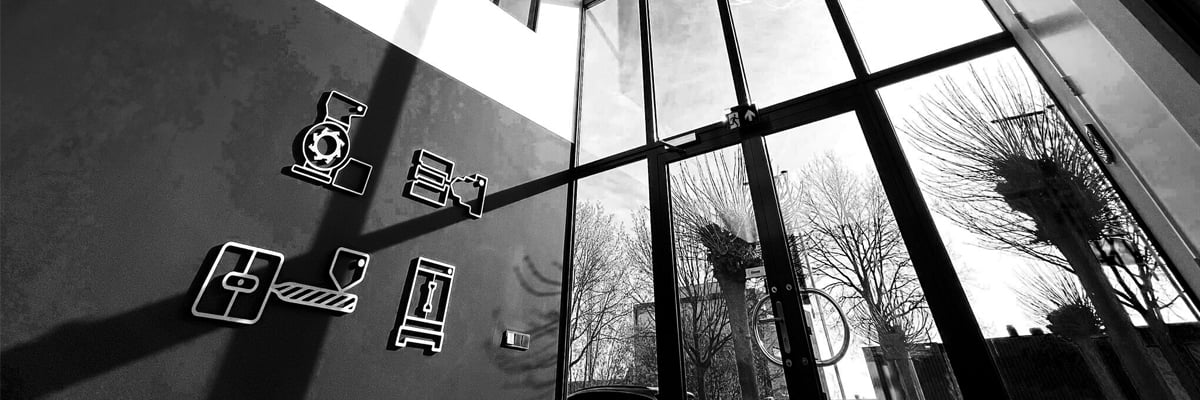
Melt pumping technology
In melt filtration in plastic extrusion, the right sieve changer for filtering process materials can be the most important solution for your extrusion line; it can make the difference between profit and loss. We list below seven reasons why installing a continuous sieve changer in a contaminated plastic extrusion line is a winning choice. Custom designing melt filtration equipment for thermoplastics that can meet the most specific requirements is not just a matter of technology; it involves strategy, production organisation and economic issues.
Melt pumping technology
Melt pumps are an essential piece of equipment in the plastics industry, used to improve the quality and consistency of polymer melts. Typically installed in the extrusion line, these pumps help increase output speed, reduce pressure fluctuations, and improve the overall quality of the final product.
Melt pumps operate with a series of interlocking gears that rotate at high speed, creating a positive displacement that pushes the polymer mass downstream through the pump and into the processing equipment. This positive displacement helps maintain a constant flow rate and pressure, which can prevent defects in the final product, such as air pockets, uneven thickness, or poor surface finish.
Melt pumps not only improve product quality but also help reduce energy consumption by enabling a more efficient extrusion process. By maintaining a constant flow rate and pressure, the extruder can run at a lower speed, requiring less energy to run the system.
In general, melt pumps are an important tool to ensure consistent, high-quality output in the plastics industry. They help improve the efficiency of the extrusion process, reduce energy consumption, and ultimately improve profits for manufacturers.
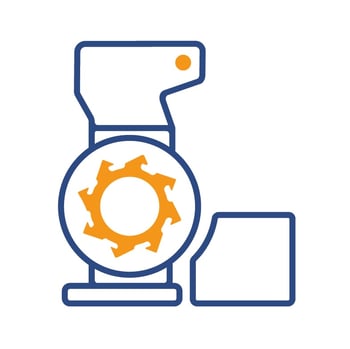
Melting pump technology at Plastima
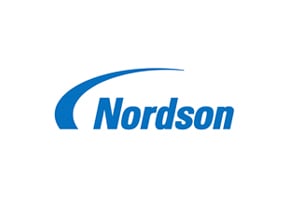
Melt pumps, also called Meltpumps, are used to keep the melt pressure higher and/or constant. In the case of underwater granulation, it can be used to increase the pressure after a co-rotating extruder/compounder. Firstly, you will then have sufficient pressure to granulate and get a nice grain. Secondly, the compounder is relieved and can do what it is for: compounding and not to have to build up pressure in the last section. Back pressure, material coming out of degassing is thus avoided.
Even in very fine filtration with a melt filter, a melt pump may be necessary to provide the necessary pressure.
Applications, where the pressure must be kept constant, include cast film extrusion, tapes, and belts, but applications where products (3D granulates) are produced with strang granulation.
If you frequently change recipes and/or colors, a melt pump in which the bearing lubrication can be flushed out is a good option.
Regarding control, there are several options that we would be happy to discuss with you. In the case of underwater granulation, we can integrate the control into the central control. Please contact Plastima for more information.

Contact-information
Contact us