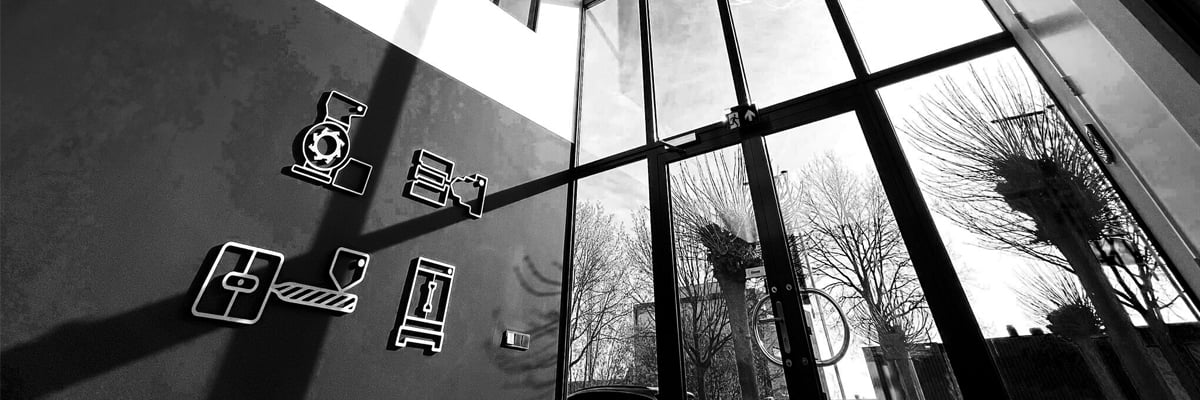
Grinding
An important step in the plastics recycling process is the grinding of the plastics. Crates, foils, packaging material, buckets, thermoforming waste, big bags, pipes with lengths of up to 6 meters et cetera. This can be production waste or post-consumer waste. All these and many other products can be shredded with equipment from our supplier AMIS.
In addition, AMIS provides expert overhaul of your shredder or grinder, of any brand. Short delivery times, parts such as complete rotors are often available from stock.
Grinding
Plastic granulators are machines used to recycle plastic waste by reducing it into smaller pieces or pellets. AMIS Zerma is a company that specializes in manufacturing high-quality plastic granulators for various industries.
AMIS Zerma's plastic granulators are designed to process a wide range of plastic materials, including hard and soft plastics, as well as larger parts and purges. The granulators are available in different sizes and configurations, depending on the customer's specific needs.
One of the main features of AMIS Zerma's plastic granulators is their high efficiency and low noise level. The machines are equipped with powerful motors and cutting blades designed to produce consistent and uniform granules while minimizing energy consumption and noise.
Moreover, AMIS Zerma plastic granulators are easy to operate and maintain. They feature user-friendly controls and interfaces, as well as easy access to the cutting chamber for cleaning and maintenance. All in all, AMIS Zerma plastic granulators are an excellent choice for any industry looking to recycle plastic waste efficiently and effectively.
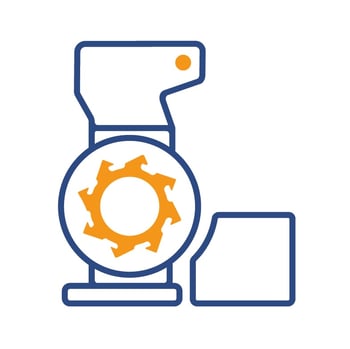
Grinding types at Plastima
A shredder is a slow-running shredder. The plastic products can be fed into the hopper; a load-dependent pressure slide ensures a controlled feed to the shaft with knife blocks. The Zerma shredders have 1 shaft, on which knife blocks of 34×34 or 60x60 mm, and counter knives coarsely reduce the plastic products.
The input material can be in almost any shape and weight. From big bags to solid start-up waste of 200 kg each, for example. The final size of the flake can be determined by the sieve placed in the shredder. Typically this is between 20 and 100mm.
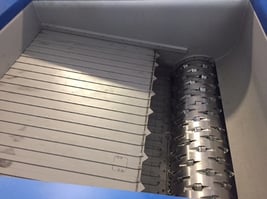
ZERMA downloads
A grinding mill, also known as a granulator, is a rotor with rotating and in the housing fixed sharp blades, which can reduce plastic products to at least a few millimeters. In the range of Zerma grinding mills, we have a lot of choices. Depending on the application, we can use slow-running mills for sprues of injection moulding machines, for example, up to large 3-meter-wide grinding mills with an output of several tonnes per hour.
Besides its specific size, each type has a rotor design specially chosen for the application. As a periphery around the mill, we can provide supply belts to the mill and extraction systems with a big bag station after the grinding mill. In this way, we have a complete milling installation, possibly supplemented with a noise-reducing enclosure, dust extraction, and/or metal detection. If the products are too large or heavy to be processed in the grinding mill in one go, they can first be coarsely pre-shredded by a shredder. This is followed by a step in 1 or 2 grinding mills to reduce the size to a few millimeters. See this set-up drawing as an example.
For recycling purposes, grinding with the addition of water is possible in a special version.
AMIS has many machines available from stock, both new and used. Naturally, we have used machines of our own house brand Zerma, but other brands such as neue Herbold, Herbold, Dreher, Tria, Getecha, Pallmann, Condux, and Rapid are also part of the range.
ZERMA downloads
The Zerma micronizing units are high-speed disc mills with fine teeth. They can grind plastics of a maximum 8 mm such as hard PVC (pipe and profile products) and LDPE millings (rotation moulding) to below 1,000 microns.
The micronizing units operate fully independently. A vibrating feeder feeds the flakes into the grinding chamber, where the grinding process takes place. After grinding, the powder is blown via a blower to, for example, a big bag station or a silo. If required, the powder can be classified via a screening machine.
ZERMA downloads

Contact-information
Contact us