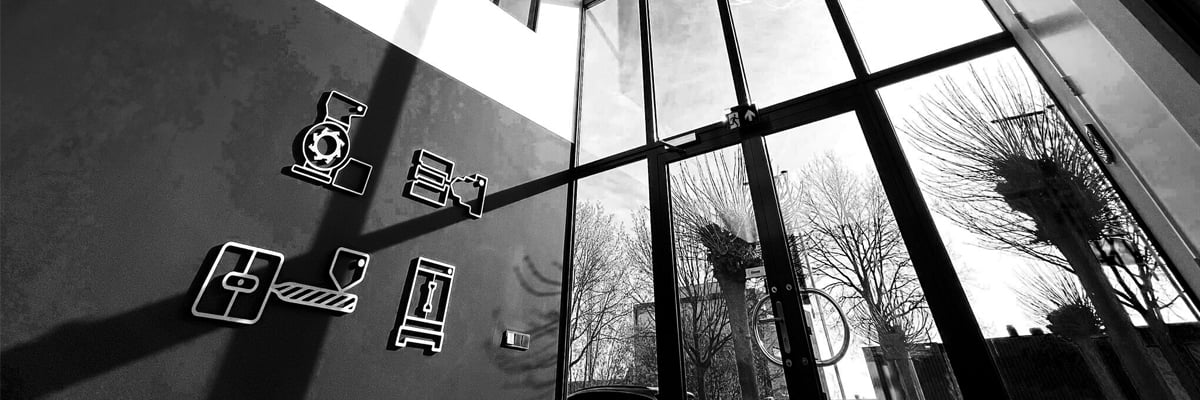
Mixing techniques
Plastima knows better than anyone else that mixing technology in the plastics industry has to meet particularly stringent requirements. Due to the huge range and variety of materials and applications, there are always new mixing tasks to be realised or recipes to be optimised. A successful end product depends on optimal mixing results. We cooperate on an exclusive basis with the renowned Kreyenborg brand. This brand has the highest standards within the mixing industry.
Mixing techniques
Plastic blending is a process of mixing two or more plastics to create a new material with the desired properties. The process involves combining the materials in a mixer, which can be a batch mixer or a continuous mixer depending on the application.
The aim of mixing plastics is to create a homogeneous mixture of the materials, with a consistent distribution of additives and fillers, and achieve a specific set of properties, such as improved strength, increased flexibility or improved resistance to heat, UV radiation or chemicals. The mixing process can be carried out using various mixing techniques, such as tumbling, ribbon mixing or high shear mixing.
Mixing plastics is an important step in the production process of plastics, as it enables the creation of customised materials that meet specific performance requirements. These materials are used in a wide range of applications, including automotive, construction, packaging and medical devices.
The quality of the blending process is important because it can affect the properties of the final plastic product. Poor mixing can lead to variations in colour, texture and mechanical properties, which can affect the performance and durability of the plastic product.

Mixing techniques at Plastima
Universal, high speed and Hot & Cold mixers
Universal mixers, High-speed mixers and hot & cold mixers are optimal tools for flexible mixing. Wherever materials need to be prepared using heat from shear forces, they deliver fast results and superior mixing quality. The mixing methods are also ideal for melting free-flowing granules. A high friction speed is achieved by peripheral speeds of 15-40 m/s, which means intensive heating of the product. The power can be flexibly controlled. All mixers at Plastima can be expanded with many additional functions and customised for individual mixing tasks, so it is a particularly cost-effective solution for customised integration into new or existing production workflows. For questions about mixers, you can always reach us!
Homogenisation mixers
In homogenisation mixing, the product is collected by the centrally located mixing screw at the bottom and transported upwards through the mixing tube. At the top of the screw, an ejector throws the material down and spreads it in fine layers over the entire section of the mixing container. The movement of the screw achieves the mixing effect through the aforementioned spreading over the entire area and through the uneven slipping of the material into the cone. For questions around homogenisation mixers, you have come to the right place at Plastima Breda.

Contact-information
Contact us